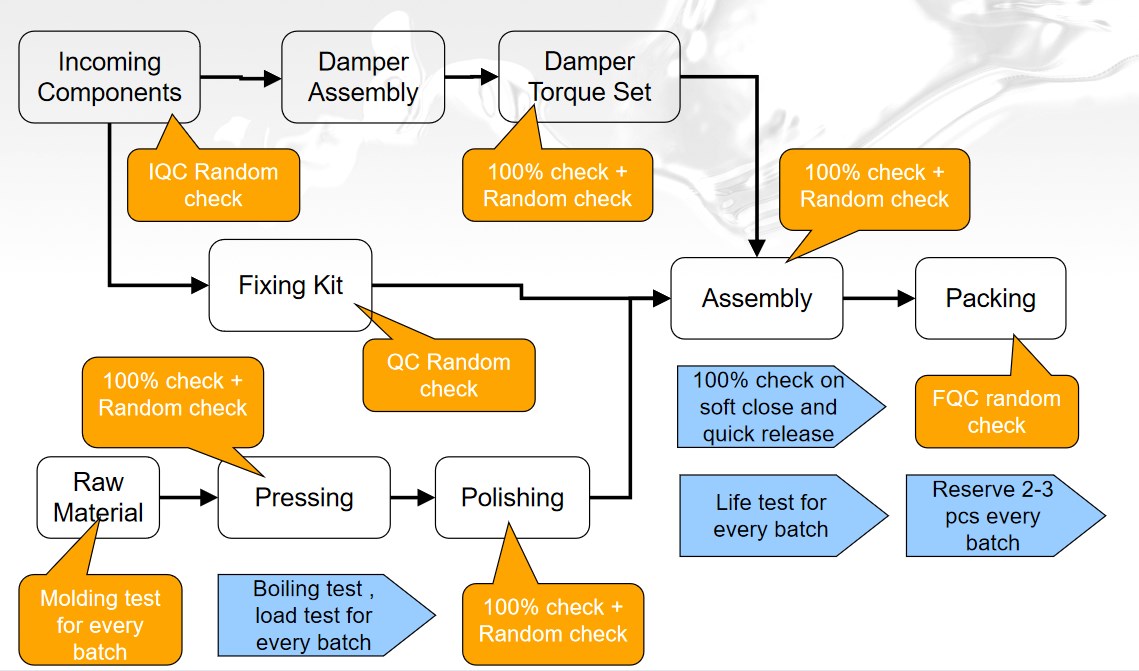
Beewill Quality Control System
In Beewill, we implement the most stringent quality management system. From above quality control flow chart, we can see that there are two main flow direction. One is for incoming components, and the other is our internal production.
Incoming components
For metal parts and smaller plastic components, we do subcontract. We will have random check when the incoming goods arrive, and then during the assembly of dampers, we 100% check the torque of every piece according to the weight of seat.
Internal Production
1. Molding test & boiling test to make sure the raw material quality
The molding process is the key process for duroplast seats, so we are paying a lot of attention to this process. Firstly we do molding test when the raw material arrives, and so to make sure the material is qualified for production. And then after the seat is molded, every seat will be checked on surface quality and structure. Besides, we also do boiling test and load test for every batch.
2. 100% check after polishing
After the molding process, we go to polishing. We polish every seat on surface and edges. This is a process to ensure a good workmanship, to make the seats friendly to touch at every point. As far as we know, we are the one who has the highest standard here. After polishing, every seat will be checked again and cleaned.
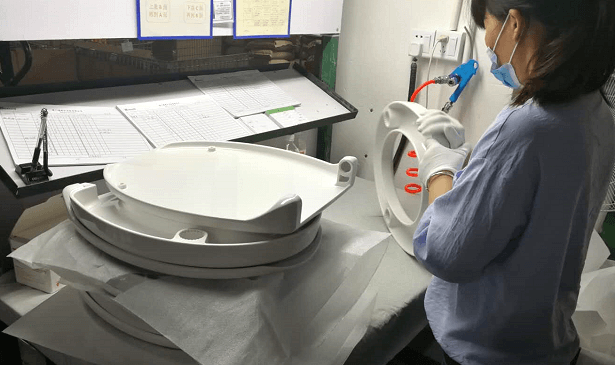
3. 100% check on soft close and quick release
After above procedures finished, the seat goes to assembly. Here we carry full check on soft close and quick release function again. As the damper is just like the heart of a soft close toilet seat, you can see actually we have checked it for twice, the 1st time before assembly and 2nd time after assembly.
4. Take the 1st piece to do life endurance test
What’s more, for every batch, we will take the first pieces from production to do life endurance test. Normally it takes 15 working days to finish 30,000 cycles. If there’s any problem, we can find it before shipment.
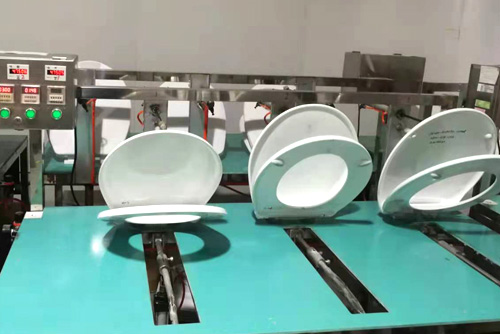
5. Random check on finished products
After packing, our FQC will do a comprehensive random check on the finished products. And take enough photos when inspection, if customers need it, we can share the photos to them directly.
6. Reserve 2-3 pcs every patch
For each batch, we reserve 2-3 pcs for at least 1 year for traceability purpose. If there is any claim in future, we can check the reserved sample right away. Also, there is date mark on the buffer housing of every seat model, so even the end user could check the production date.
We can see that there are 8 x 100% check for key procedures. For those customers who do not arrange inspection, we can also send them our internal inspection reports.